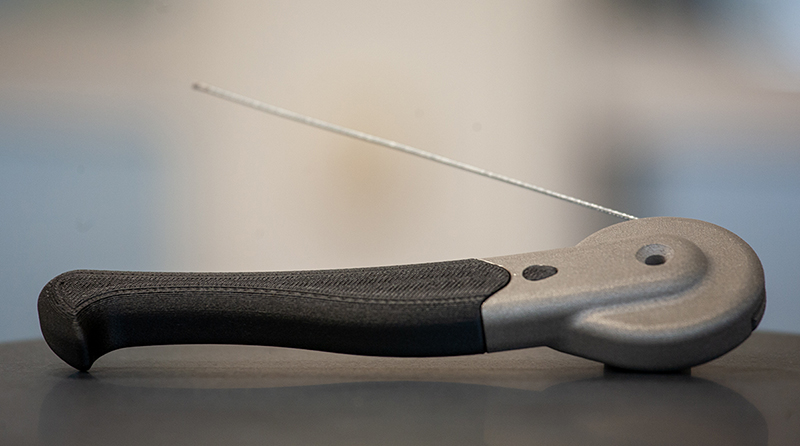
Ett projekt om ett handtag, från designskiss till en fullt fungerande produkt med additiv tillverkning. Genom att använda additiv tillverkning och innovativ konstruktion blir resultatet produkter som väger mindre och kostar mindre att producera.
För ett tag sedan fick Protech en fråga från en av sina partners: kan ni konstruera ett handtag från en designskiss? Handtaget skulle först tillverkas som en prototyp och senare i en mindre volym om fem handtag. Den slutgiltiga volymen av tillverkade handtag skulle bli 100 stycken per år. Handtaget behövde vara lätt och därför föreslogs Aluminium.
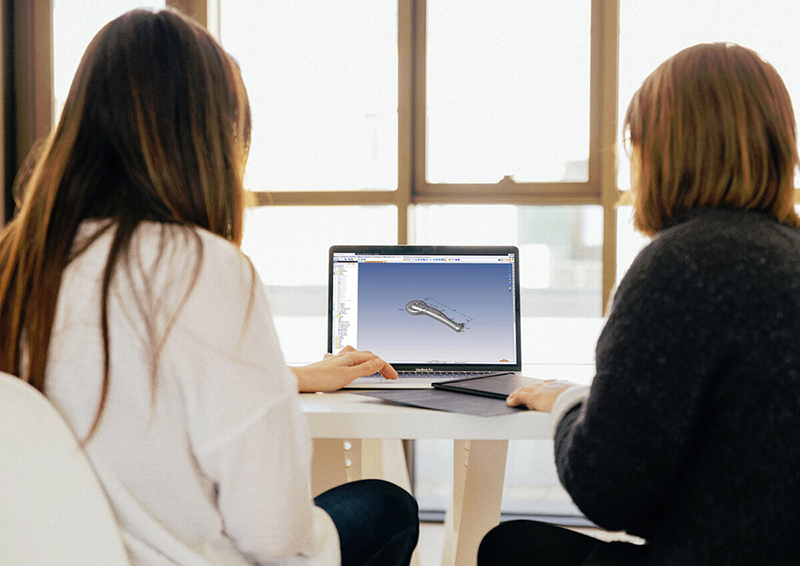
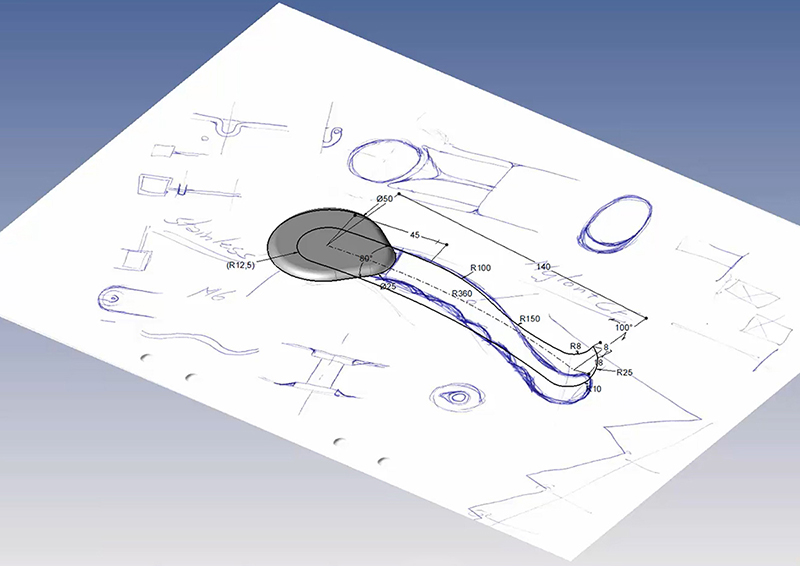

Fräst handtag i Aluminium
Vår partner ville att handtaget skulle ha en slät yta för att underlätta rengöring. Kravet gjorde att vi inte kunde göra produkten lätt genom ribbor och hål från utsidan på handtagsytan. Den första konstruktionen tog 12 timmar från skiss till färdig CAD-fil och utfördes i det integrerade CAD/CAM-systemet TopSolid’Design. Efter färdig konstruktion gjorde vi CNC-programmering i TopSolid’Cam och påbörjade bearbetningen. Det färdigfrästa handtaget blev riktigt bra men krävde en hel del manuellt arbete. Vi tog bort handtaget från fräsblocket, fixade till ytorna och blästrade sedan hela ytan. Det färdigfrästa handtaget vägde 187,5 gram.
Frästiden för det första handtaget var ganska lång. Det är förväntat när det gäller fräsning av en första prototyp då det ofta krävs en hel del verktygsriggande och omprogrammering av NC-koden innan maskinoperatören blir helt nöjd. Första fräsningen tog 8 timmar och kostnaden inkl. material, CNC-programmering och maskintid blev 807 euro. Nästföljande fräsning av ett handtag tog 1 timme och 25 minuter och det fanns säkert en del till att göra för att trimma ner den tiden i maskin. I tabellen längre ner kan du se kostnader och produktionstid för några olika produktionsvolymer.
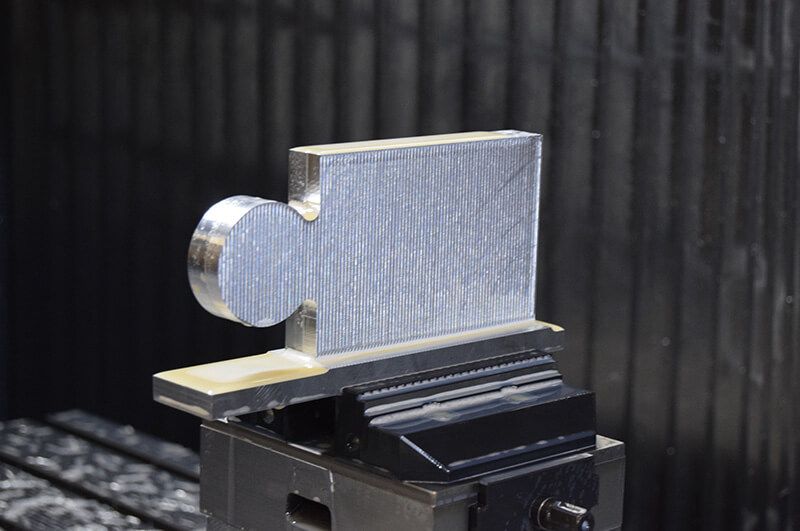
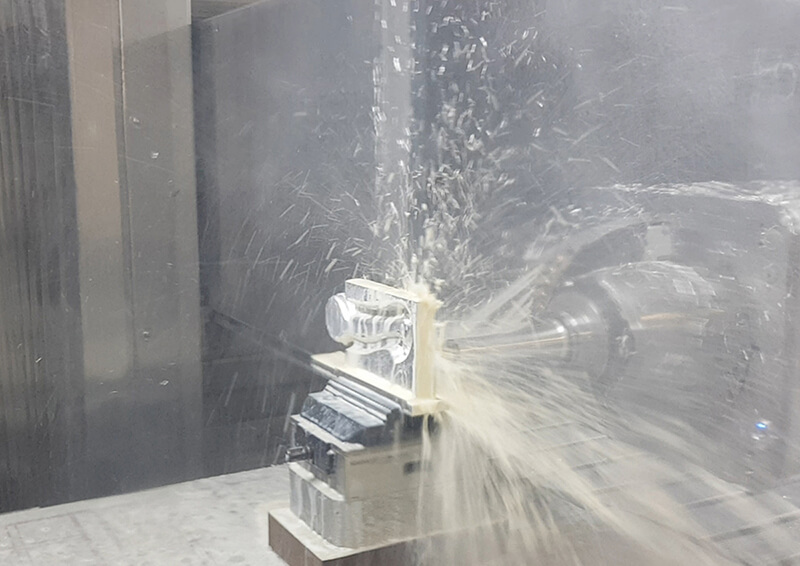
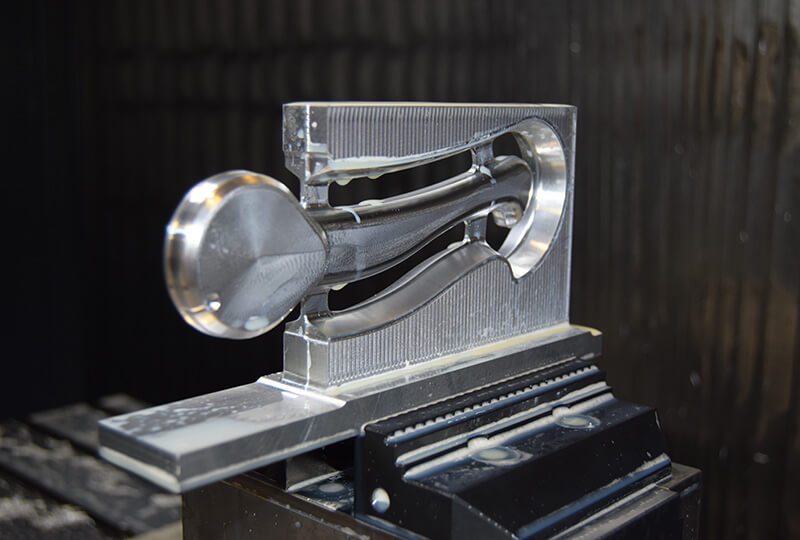
Varför inte använda additiv tillverkning?
Efter att vi analyserat det frästa Aluminiumhantagets vikt och produktionskostnad ställde vi oss frågan – varför inte använda additiv tillverkning och tillverka ett ihåligt handtag i rostfritt stål? Kraven på handtaget var sådana att infästningsdelen av handtaget behövde vara i metall men inte nödvändigtvis i Aluminium.
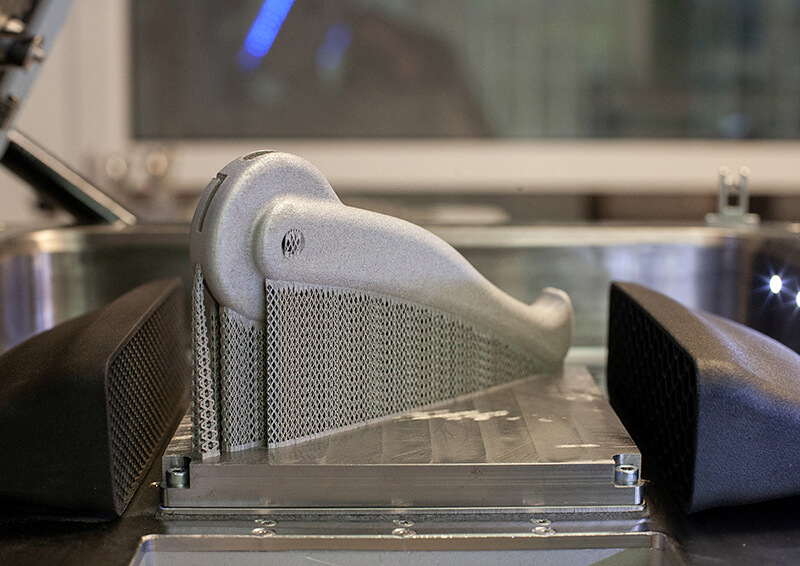
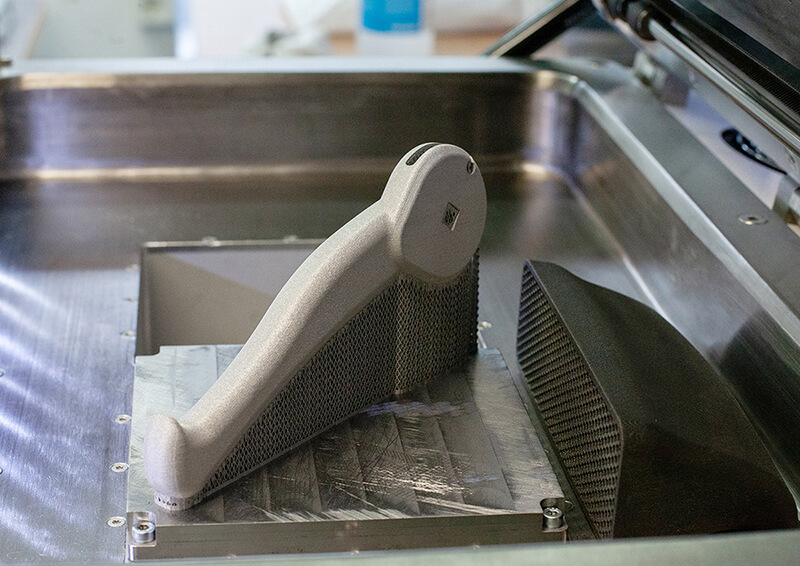
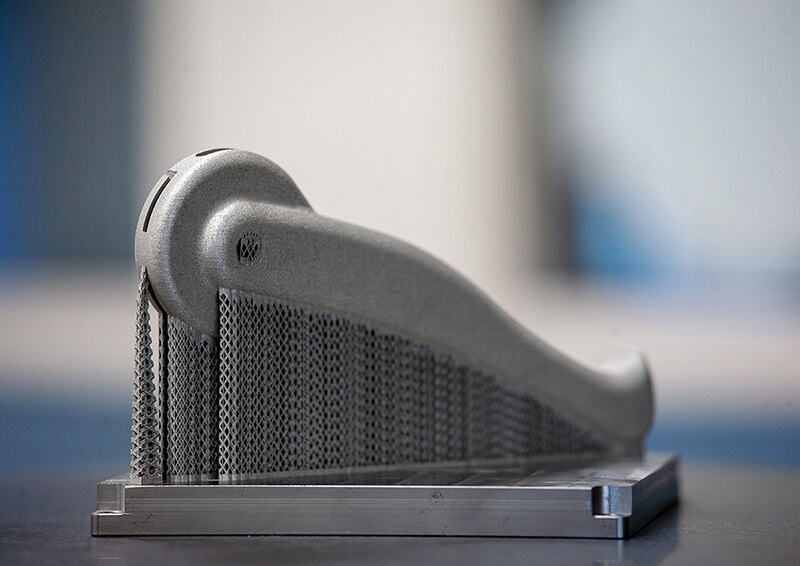
Vi valde att tillverka det ihåliga handtaget i rostfritt stål (316L), istället för Aluminium, då maskinkostnaden för att producera med additiv tillverkning är betydligt lägre i rostfritt stål än i Aluminium. Tillgängligheten av produktionskapacitet för additiv tillverkning i rostfritt stål är dessutom betydligt större än i Aluminium. Den ursprungliga handtagskonstruktionen gjordes ihålig med en godstjocklek på 1 mm. Vi la även till ett litet hål för att få ut överskottspulver ur handtaget. Det tog mindre än 5 minuter i CAD-systemet att utföra de två justeringarna. För att kunna 3D-printa ett komplett handtag var vi tvungna att lägga till stödstruktur. Generering av stödstruktur är en förhållandevis automatisk process. Generering av stödstruktur till det kompletta handtaget tog 15 minuter. Det tog 43 timmar och 11 minuter att skriva ut det ihåliga handtaget i vår Xact Metal XM200C. Byggvolymen i XM200C begränsade oss till att skriva ut ett handtag i taget.
Borttagning av stödstruktur efter 3D-utskrift med Metal Powder Bed Fusion (Metal-PBF) är i många fall ett tidsödande arbete. För en detalj liknande vårt handtag görs borttagandet i de festa fall manuellt. 3D-utskriften av det ihåliga handtaget blev riktigt bra och med en vikt på 112,2 gram. Vikten på handtaget var nära målet på under 100 gram men kostnaden per handtag var för hög och produktiviteten blev för dålig. Även om man skulle använt en maskin med större byggyta och i den kunde skriva ut fler detaljer samtidigt blev produktiviteten för låg.
Kolfiberförstärkt Nylon gav styrka i handtaget
Utmaningen var att sänka vikten på handtaget utan att tumma på konstruktionskraven. Infästningsdelen av handtaget behövde vara i metall men vad händer om man kombinerar plast och metall? Med en tvådelad konstruktion kunde handtagsdelen tillverkas i plast vilket drastiskt sänkte vikten på hela handtaget. Omkonstruktion av handtaget till en tvådelad produkt tog 8 timmar.
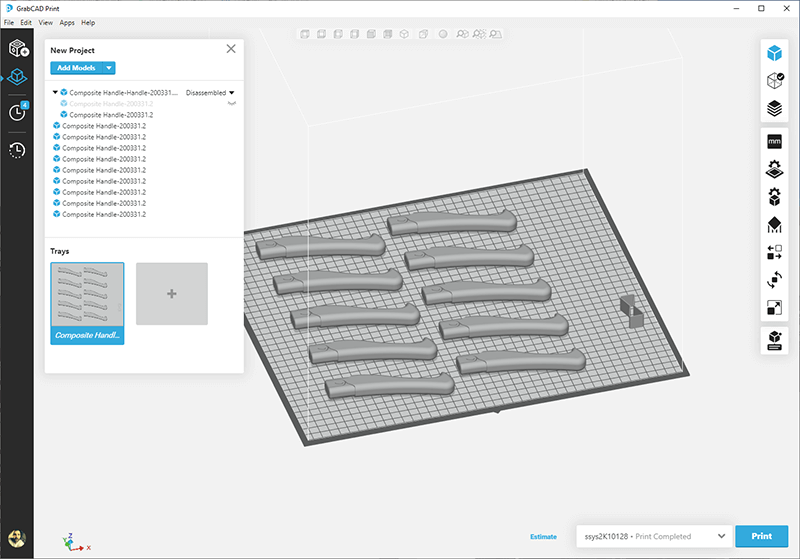
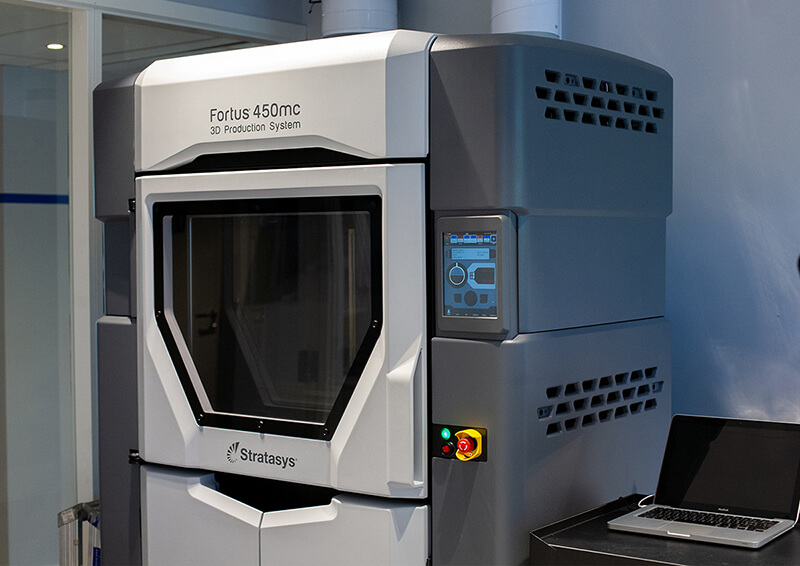
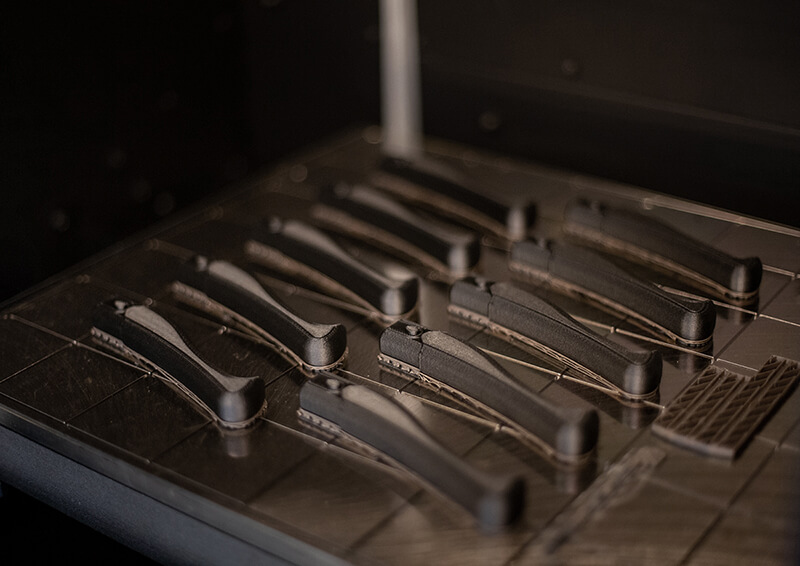
Handtagsdelen av det tvådelade handtaget konstruerades så att det kunde 3D-printas i kolfiberförstärkt Nylon (Nylon 12CF) i vår Stratasys 450mc 3D-skrivare. De mekaniska egenskaperna för materialet är enastående och detaljen gick att skriva ut med en invändig så kallad Lattice-strukture. Tio handtagsdelar fördelades på 3D-skrivarens byggyta och skrevs ut på 7 timmar och 36 minuter. En enstaka handtagsdel tog 1 timme och 10 minuter att skriva ut och hade en totalvikt på 25 gram.
Infästningsdelen utskriven i Xact Metal
Infästningsdelen av handtaget konstruerades för att korta ner utskriftstid och behovet av stödstruktur. Tio infästningsdelar kunde packas på byggplattformen till vår Xact Metal XM200C och tog 125 timmar och 10 minuter att skriva ut. Borttagande av stödstruktur och färdigställande av varje detalj tog dock tid. Varje detalj blästrades sedan för att få en jämn ytstruktur. En infästningsdetalj tog 17 timmar att skriva ut och vägde 60 gram.
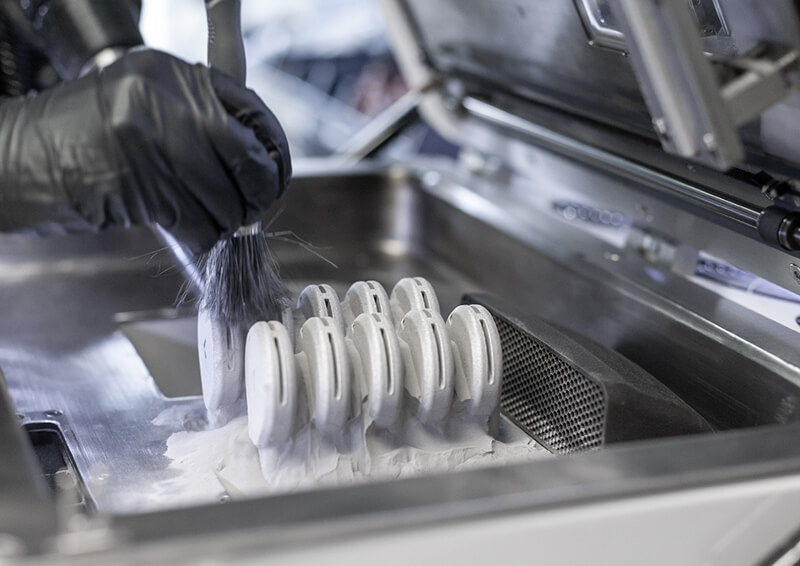
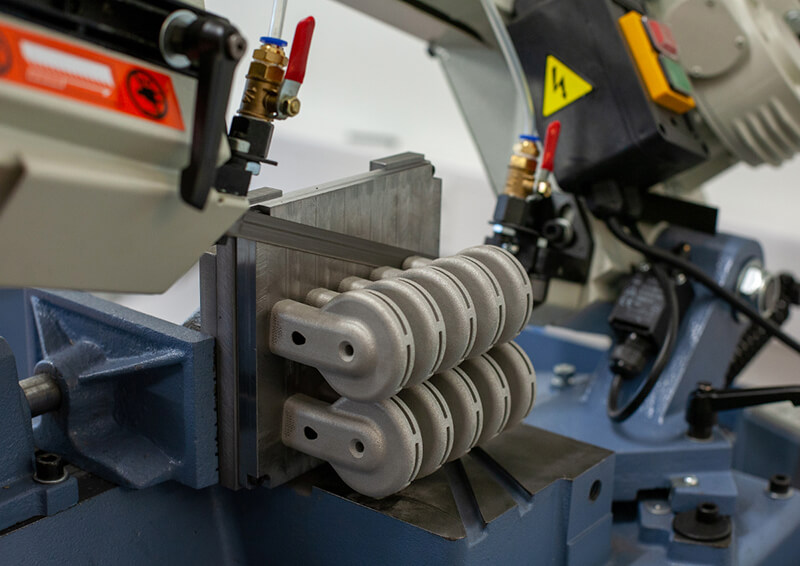

Ett komplett handtag på 85 gram
Det tvådelade handtaget fick till slut en totalvikt på 85 gram, vilket betydde lägsta vikt och lägsta produktionskostnad av alla de varianter av handtag som producerades i projektet.
Genom att använda additiv tillverkning och innovativ konstruktion blir resultatet produkter som väger mindre och kostar mindre att producera. Konstruktion för additiv tillverkning utmanar konstruktörer att tänka i andra banor men kan resultera i bättre produkter än med traditionell tillverkningsteknik – tänk additiv tillverkning.
Kostnadsöversikt
Tabell som redovisar kostnad och tid för tillverkning 1, 10, 25 och 100 av de olika handtagsvarianterna.
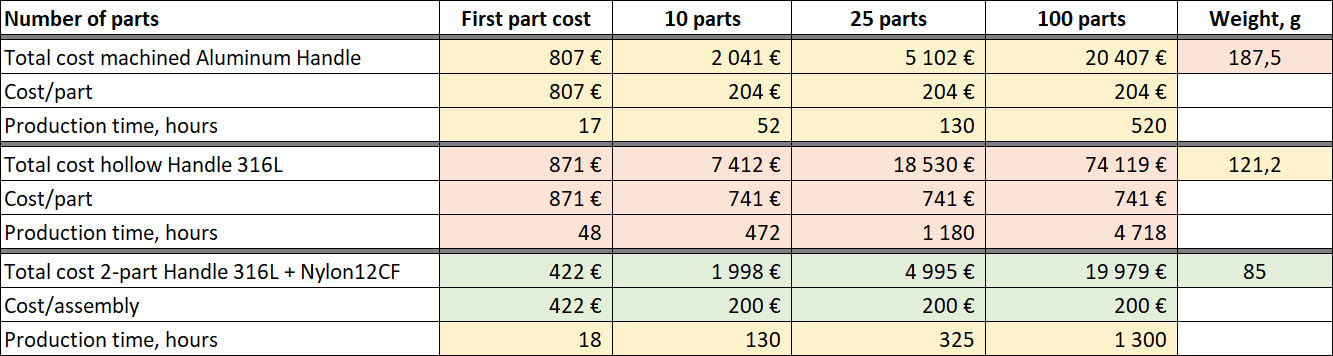
Kostnaderna redovisade i tabellen är faktiska kostnader i Sverige. Självklart är det så att beräkning av tillverkningskostnader varierar land för land. Manuellt arbete är en stor del av kostnaden för de olika varianterna av handtagskonstruktion och kostnaden för manuellt arbete varierar väldigt mycket mellan olika länder. I tabellen redovisas kostnader och inte det faktiska priset på ett tillverkat handtag. Företag som tillverkar produkter lägger alltid på marginal på sina produktionskostnader. Vilken marginal som läggs på varierar väldigt mycket mellan olika företag. Därför kan det faktiska priset på en produkt variera en hel del.
Alla de slutsatser som dras i detta projekt är helt och hållet geometriberoende. En annan produkt med en annan konstruktion kommer troligen att resultera i andra slutsatser.
Protech har tillåtelsen att publicera detta projekt för att inspirera andra att fundera på hur deras produkter tillverkas. Projektet får fritt användas och modeller samt underliggande beräkningsdata kan rekvireras av Anders Brask (kontaktuppgifter finns längst ner).
Sänkt vikt på en produkt sparar kostnader, minskar en produkts klimatavtryck samt dess transportkostnader. Additiv tillverkning kommer att spela en viktig roll i förändringen av hur produkter är tillverkade.
Kontakta en av våra säljare för mer information
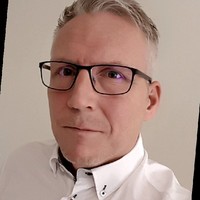